3月28日,中国首个重卡数字孪生智慧工厂落成投产暨北京重卡首台车下线仪式在北汽重型汽车有限公司举行。北汽重卡是北汽集团“十四五”期间京外重大投资项目的重要落子,北汽重卡数字孪生智慧工厂落成投产和北京重卡首台车下线,标志着北汽集团在重型商用车领域进入了南北布局的全新发展时代。
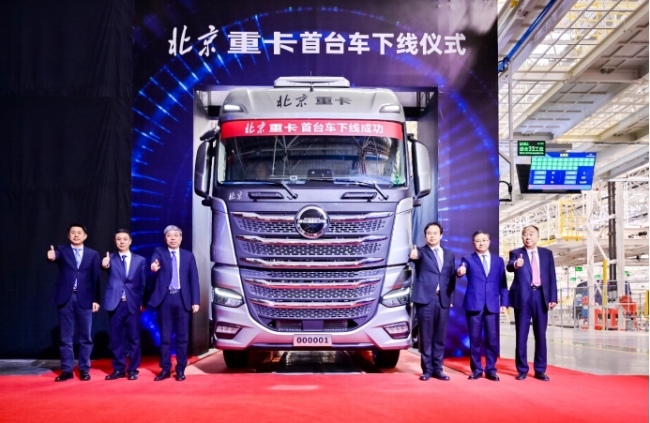
北京重卡首台车下线
北汽集团党委常委、副总经理蒋自力表示,北汽集团将全力支持北汽重卡坚持战略引领和创新驱动,直面市场竞争,不断提升客户体验,为领跑中国商用车市场奠定坚实基础。
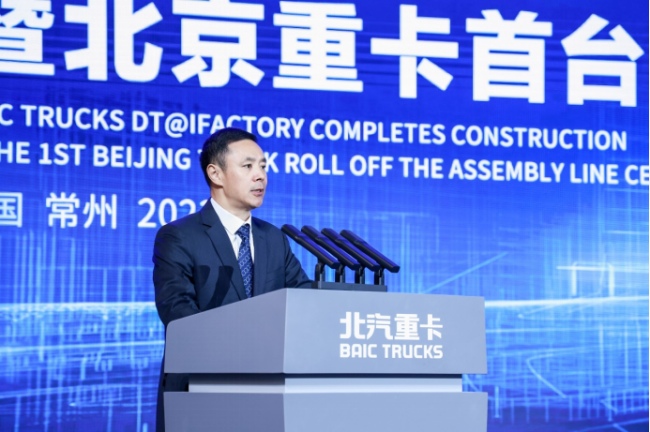
北汽集团党委常委、副总经理蒋自力
“北汽重卡将以世界级重卡产品梦,实现客户辛勤劳动的致富梦。”北汽重卡党委书记、总经理吴越俊表示,过去三年里,北汽重卡积极拥抱数字化,在商用车行业率先建立中国首个数字孪生智慧工厂,致力智能化和数字化应用。
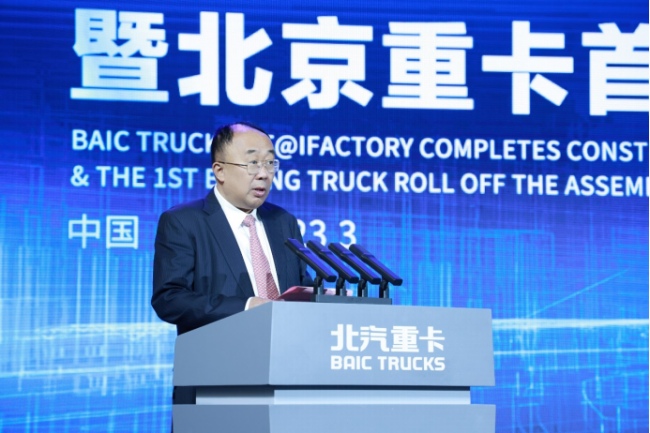
北汽重卡党委书记、总经理吴越俊
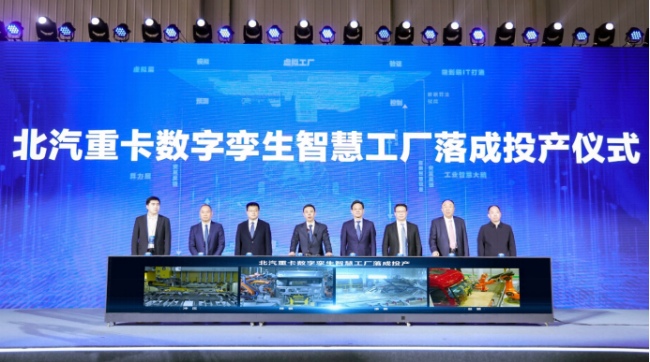
北汽重卡数字孪生智慧工厂落成投产
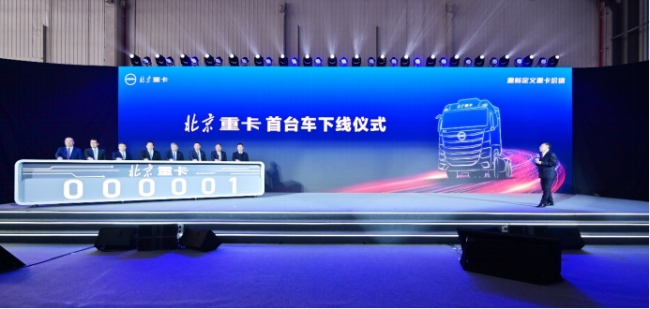
北京重卡首台车下线
当天,北汽重卡新能源验证中心同时揭牌,该中心投资15亿元,将为常州新能源建设及北汽重卡针对不同场景制定不同新能源产品开发策略按下“加速键”。
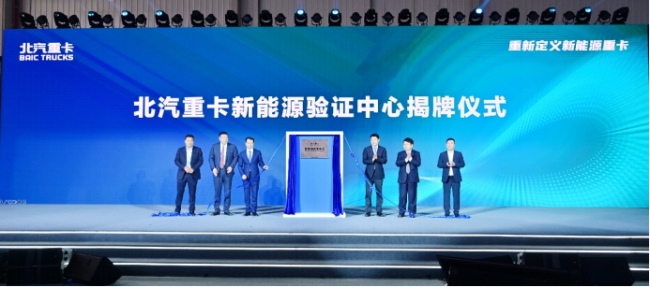
北汽重卡新能源验证中心揭牌
与此同时,北汽集团也早已启动了对未来技术市场的布局。“北汽重卡将针对用户不同场景制定不同的新能源产品开发策略,以多技术路线全面布局新能源。新能源是北汽重卡的重要战略,北汽重卡将开发一代,预研一代,多技术路线全面布局新能源。”北汽重卡副总经理兼营销公司总经理薛善仓讲解了北汽重卡新能源战略发展规划。据悉,北汽重卡新能源业务定位在“纯电、混动、燃料电池”三条技术路线全面推进,未来自主掌控“电池、电驱、电控”核心技术。
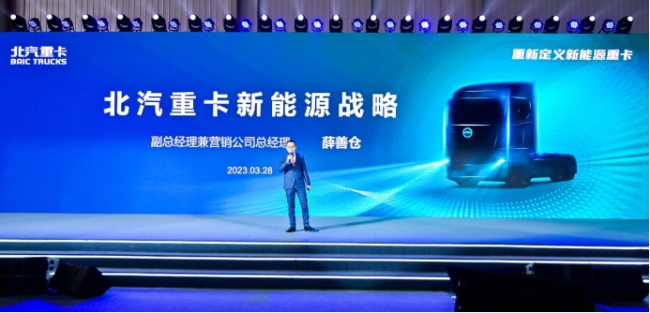
北汽重卡副总经理、营销公司总经理薛善仓讲解新能源战略规划
活动现场,北京重卡首台车下线即交付客户,首批客户代表从北汽重卡营销公司副总经理杜昌伙手中接过了车钥匙。
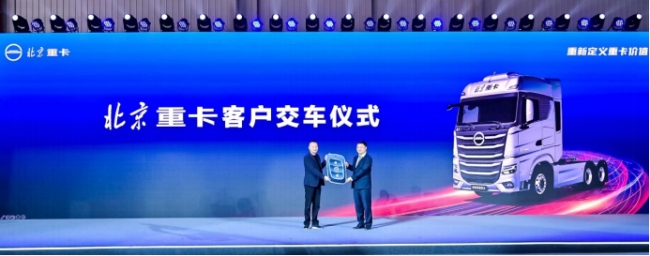
北京重卡客户交车仪式
解码中国首个重卡数字孪生智慧工厂DT@iFactory
目前,北汽重卡积极拥抱数字化,在商用车行业率先建立中国首个数字孪生智慧工厂。依托数字孪生技术,北汽重卡在行业内首次建立工厂数字孪生体,新工厂设计之初从厂区规划到设备调试,完全在虚拟孪生模型中进行创建模拟。通过在物理工厂部署数以万计的传感器,依托数据镜像再现虚拟工厂,对全域感知,实现IT与OT的完美融合,以数字孪生技术实现以虚预实,以虚优实,真正实现以数字化赋能智能智造。
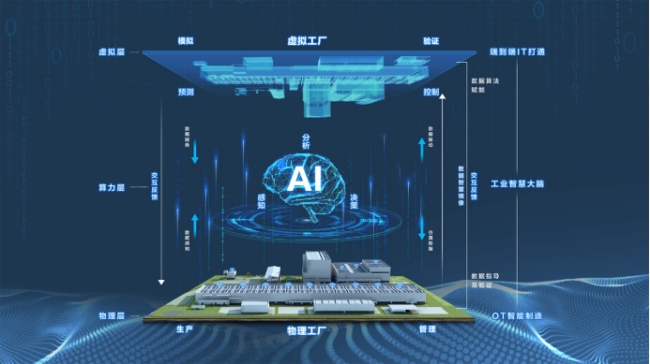
北汽重卡数字孪生智慧工厂
“端到端”全过程透明化
凭借高度的数字化,北汽重卡数字孪生智慧工厂首次在行业实现了“端到端”的革命。将客户端、产品端、供应商端与工厂端全面数字化打通,并在各端高效精确传递。北汽重卡首创全配置BOM+用户点单,OTD订单准时交付系统实现订单端到端打通,全过程透明可参与,把用户从消费者变成产消者。
围绕工人、工程师、供应商“三类人”,数字化驱动的AQMIS质量管理集成系统打通市场、研发、供应链、制造等全价值链质量信息流,实现质量问题同步响应,产品全生命周期可追溯。
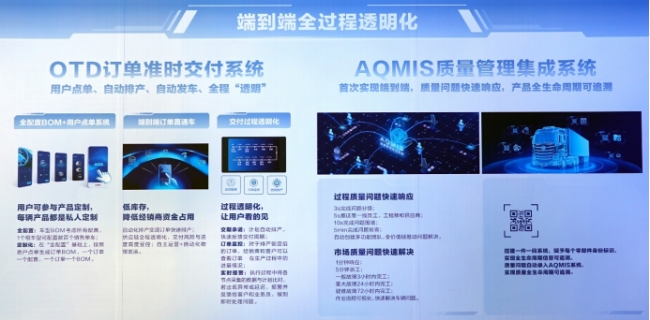
端到端全过程透明化
大数据和智能算法实现了排产、库存、人力资源等生产要素的最优配置
以端到端打通的海量数据为基础,以智能算法驱动,北汽重卡数字孪生工厂实现了APS智能排产、智能库存、智能人力资源配置和智能防错等四大优势,全面提高了资源利用率,创造了新价值。
智能排产——通过APS智能排产策略,智能算法得出排产结果,并通过KPI评估与调整,循环优化升级,实现成本最低、库存水平最优、效率最高、交付周期最短。
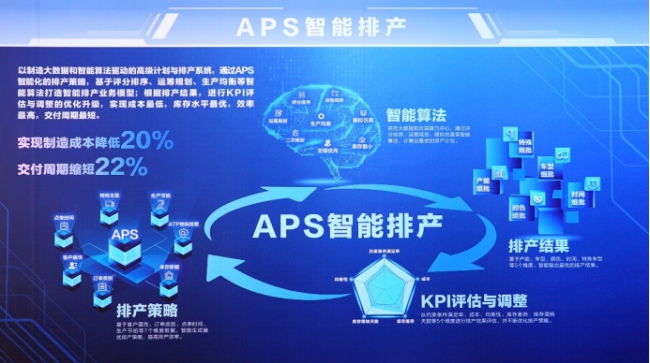
APS智能排产
智能库存——打通工厂和零部件供应商订单系统,利用二维码技术,为每一个零部件赋予唯一的身份序列号,实现对每个零部件全生命周期信息可追溯。打通厂内外零部件物流,基于智能物流算法,分析得出最优零部件生产量和物流及存储方案,零部件直配厂家RDC库,甚至直配产线,取消VMI周转库,极大降低零部件库存的同时满足零部件交付0延误。
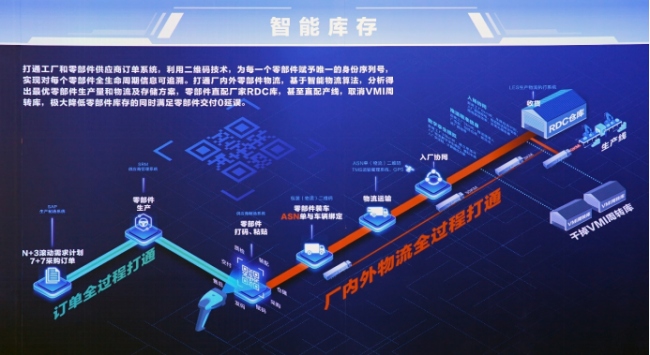
智能库存
智能人力资源配置——以数字化智能工位为核心,打通“人、机、料、法、环”等数据端,通过智能算法,生成最优的人员资源配置方案,从而实现智能工位安排、智能排班、精益工时及智能人员优化,实现人力成本降低5%,线平衡率提升5%,员工满意度100%。
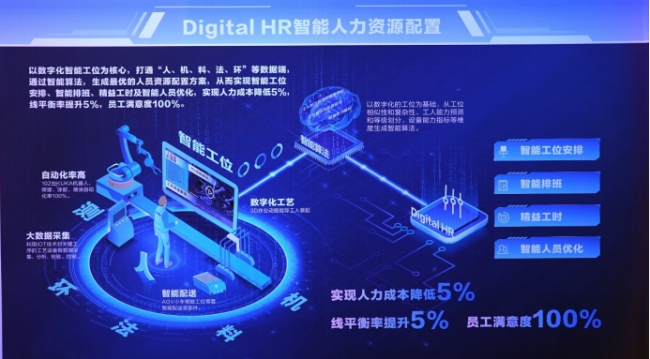
Digital HR智能人力资源配置
72道智能工艺防错——依托BOM、MEDS、MES、AQMIS四大数字系统,在产线作业环境下设置了72种防错机制,让装配出错成为不可能,真正做到了交付给用户的产品“0缺陷”。
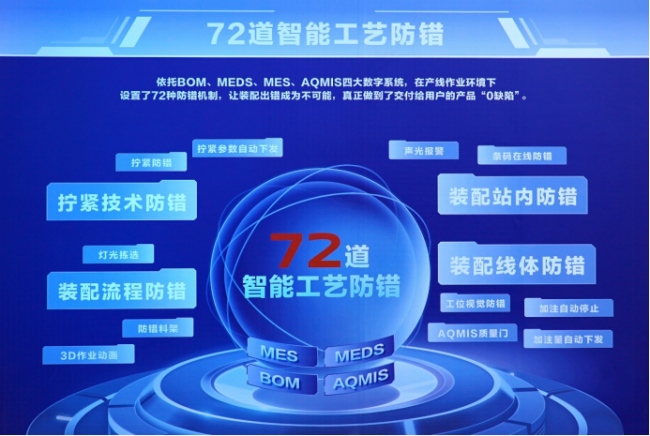
72道智能工艺防错
数字化四大工艺
北汽重卡数字孪生智慧工厂以数字孪生技术赋能“冲焊涂总”四大工艺,不仅实现多项行业首创技术的诞生,更将工厂全自动化率提升70%,引领重卡智造全面革新,比肩国际领先水平。
超高精度全自动冲压车间——全工序100%自动化生产,拥有重卡行业首创全自动360°蓝光智能扫描设备,引入了世界一流的6600T超高精度冲压生产线和数字化离线模拟系统。
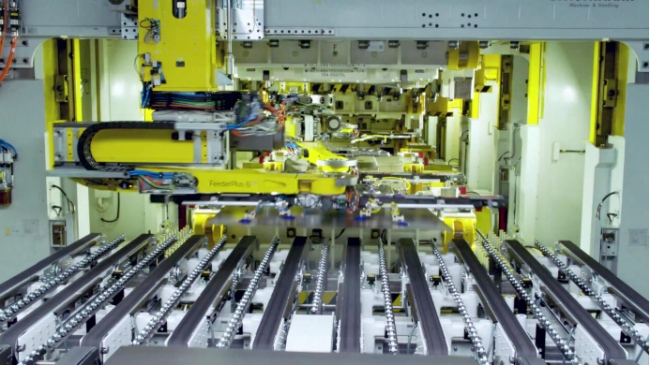
超高精度全自动冲压车间
数字化全机器人焊装车间——采用行业最高水平的全数字化设计仿真技术,AI视觉在线100%精度检测,应用数字化仿真技术的德国KUKA机器人焊接强度合格率高达99.8%。
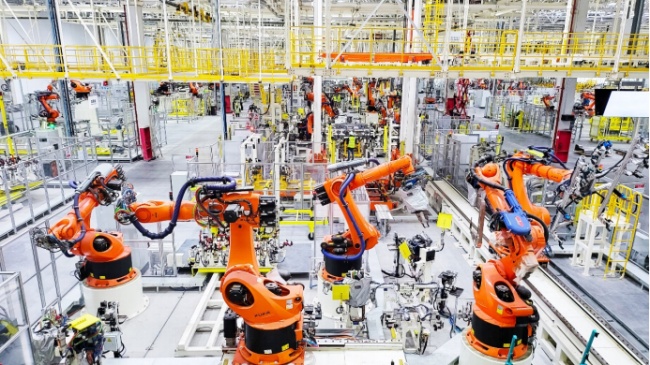
数字化全机器人焊装车间
全自动化无人涂装车间——集中了行业先进的前处理电泳工艺,独有的底盘整体喷涂工艺和领先的中面涂工艺,底盘件喷涂覆盖率100%,防腐更全面。
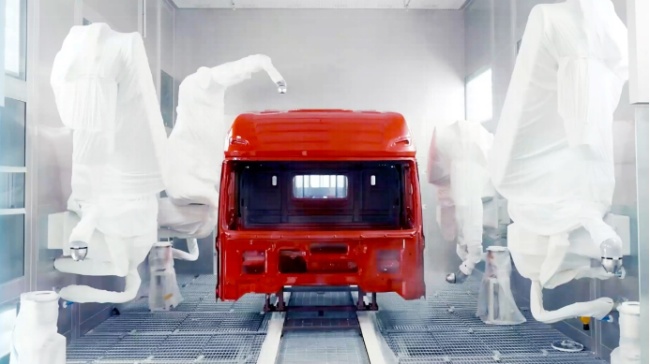
全自动化无人涂装车间
数字孪生智慧总装车间——以全配置化BOM为核心将数字化配置到工位,通过构建数字孪生车间,为用户提供高质量、0缺陷的个性化定制产品。
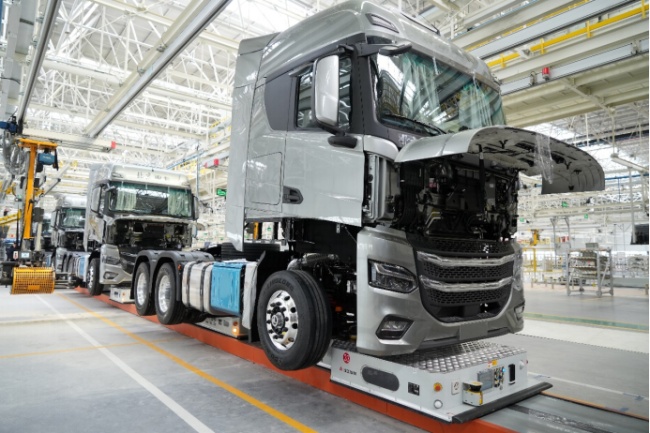
数字孪生智慧总装车间
以数字孪生技术为依托,以全面的数字化赋能智能制造,北汽重卡数字孪生智慧工厂让以用户为中心的“高质量低成本”战略真正落地,也成为北汽重卡未来参与国内、国际市场竞争的底气所在。
数字孪生是实现数字化转型的核心竞争力,北汽重卡建立的首个数字孪生智能工厂,实现数字驱动,端到端打通,让用户参与,把消费者变成产消者,创造了新模式、新体系、新价值。
基于数字化技术,相较于传统制造方式,北汽重卡数字孪生智慧工厂实现了单台成本降低20%,质量提升22%,交付周期缩短22%,交付满意度达到100%。
全新一代聪明的北京重卡为客户创造新价值
全新一代北京重卡应用数字技术构建重卡数字孪生模型,通过三重验证,充分解决研发环节的质量问题,在车辆交付运营后,应用孪生伴跑技术,收集用户运营及车辆行驶等数据,对产品进行优化,通过OTA实现快速迭代升级,从而建立数字孪生研发闭环。依托根魔方和超级BOM创新,实现场景定制。以数字科技打造i-Beijing北京重卡,实现智能节油和智能安全,从而让用户的梦想触手可及。
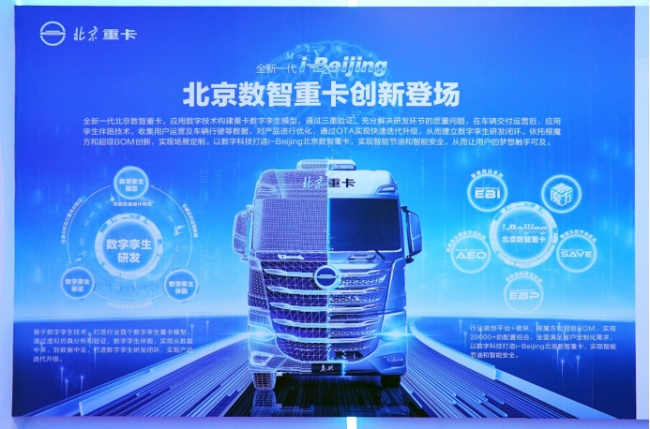
基于数字孪生技术,北京重卡打造行业首个数字孪生重卡模型,通过虚拟仿真分析和验证,数字孪生伴跑,实现从数据中来,到数据中去,打造数字孪生研发闭环,实现产品迭代升级。同时,以“数智”为基因,北京重卡产品研发历时近300天,深入121个城市和地区浸入式调研打造用户数字模型,精准洞察用户需求,实现精准研发。
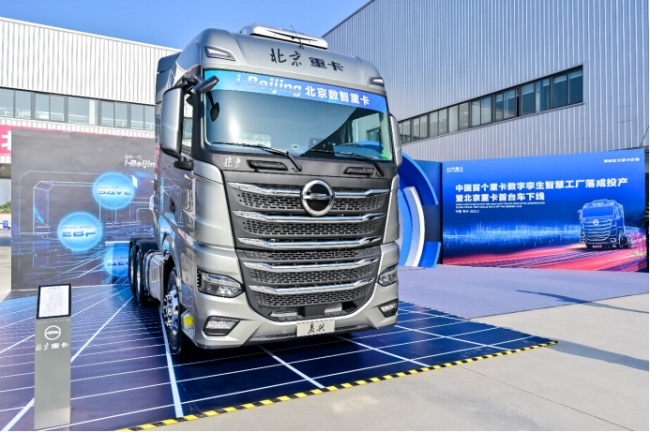
北汽重卡首创用户点单系统,通过“平台+模块”、根魔方、EBOM的智能匹配,实现超20000+种产品配置组合,满足用户的个性化定制需求,自由选配,让每一台车都是私人定制。
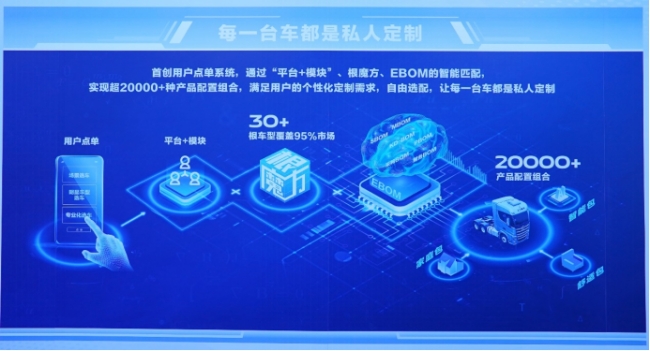
凭借Smart AEO智能自主寻优节油系统、Smart SAVE智能云控节油系统、Smart EBP智能油耗管理系统、Smart EBI智能制动系统4大“Smart”核心系统加持,北京重卡在实现智能节油与智能安全的同时,每年可以节省油费48600元,节省维保费用47000元。高质量的北京重卡可以达到月出勤大于28天,一年多出勤一个月,一年多赚30000元,预计全年创造价值可达130000元。
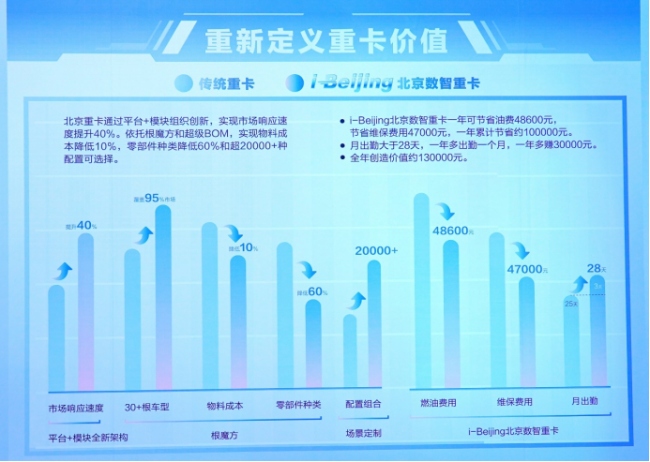
智慧工厂智造高质量 北京重卡收获503台信赖
“我们创建新型数字化工厂,将客户端、产品端、供应商端与工厂端全面打通,所有生产要素实现数字化,并在各端高效精确传递。同时,通过大数据和智能算法实现了排产、库存、人力资源、防错等生产要素的最优配置,真正做到了数字化赋能智能制造。最终实现单台成本降低20%,质量提升22%,交付满意度达到100%。”北汽重卡党委书记、总经理吴越俊在现场受访时表示。
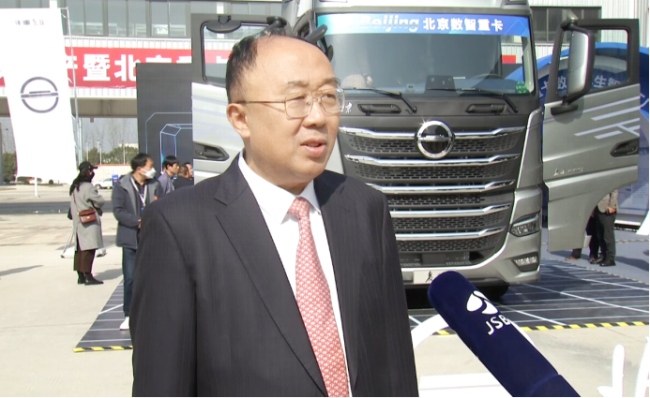
北汽重卡党委书记、总经理吴越俊接受现场媒体采访
北京重卡首台车下线即交付客户,目前,北京重卡首批客户预售订单已达到503台,也进一步印证了客户对北京重卡的信赖和期待。
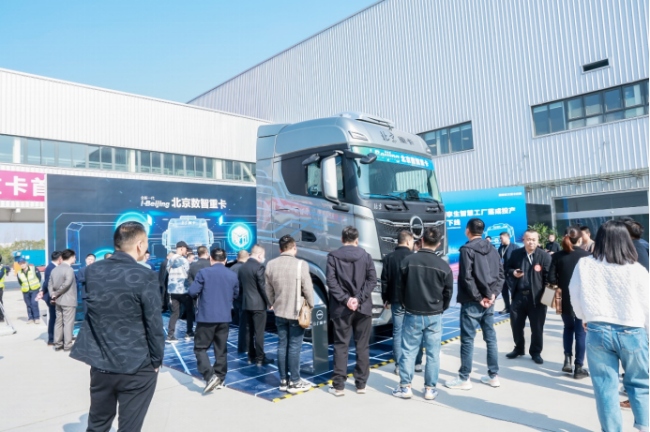
客户参观品鉴北京重卡
北汽重卡始终坚持把质量放在第一位。全新一代北京重卡已完成累计超过1千万公里的实际道路验证和1亿3千万公里的数字虚拟验证。同时,北汽重卡600余家服务站已经培训完成,超过千万元储备配件也已陆续投放市场,客户可放心购买。
北汽重卡坚持以用户为中心,创新驱动,数字赋能,无论是中国首个重卡数字孪生智慧工厂的创建,还是以用户思维全新架构创新打造的全新一代i-Beijing北京重卡,都创造了新模式,新体系,新价值,将引领中国重卡行业的产业升级,为物流行业提供升级版的降本增效解决方案,也会以卓越的价值受到用户的热捧。